The most modern technology available to the foundry industry
The first step of the foundry project started several years ago when initial discussions with DISA commenced.
As the talks proceeded, and the plans became increasingly defined, it became evident that Macedonia should be the spot in which to place this EUR 15 million green field investment.
“We never doubted that we should deploy the most modern technology available in the foundry industry. And through our numerous talks with representatives and experts from DISA, we reached the conclusion that the DISA MATCH 32/32, offering high precision, flexibility and quality, as well as the DISA complete sand plant solution would be the best and most modern foundry technology choice for our new plant”, Dariusz Dziuba says.
Challange
Building one of the most modern foundries in Europe
“Our main challenge is to build the most sophisticated, highly automated and eco-responsible foundry for car parts manufacturing.
Our plans are being shaped constantly, as we continuously seek to improve our business focus to meet customer needs and changing market conditions.” Dariusz Dziuba explains.
“We believe that DISA Industries – being the global leader of foundry technology – and DISA state-of-the-art equipment, tools and techniques will help us to provide consistent and high quality products to our customers.
More concisely, we view the DISA MATCH 32/32 moulding line as well as the DISA complete sand plant solution to be the best and most future-oriented choices for CRANFIELD." Mr. Dariusz Dziuba, CEO at CRANFIELD Foundry
Solution
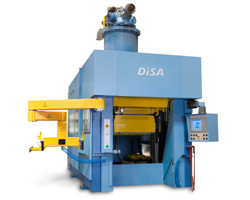
1st deliveries in early 2017
“Our customers expect the first CRANFIELD deliveries to hit the market sometime during the 2nd quarter of 2017.
We expect that the DISA MATCH 32/32 flaskless moulding line together with a custom-made DISA sand plant will help us to achieve a casting quality and productivity that will more than match our expectations”, Dariusz Dziuba states.
"Our aim is to build one of the most modern foundries in Europe, and for that purpose, we have chosen DISA as our key foundry supplier and partner."
Result
Other than expecting to create up to 280 jobs with the new foundry, CRANFIELD has equally high expectations when it comes to the equipment commissioned:
“DISA is a worldwide recognized brand that has shaped the foundry industry for years. Associating DISA with both the highest possible level of quality and reliability as well as highly automated processes, we have made it no secret that we expect to reach an annual production capacity of 10,000 tonnes – and a DISA MATCH 32/32 mould speed of 100 m/ h”, Dariusz Dziuba concludes.